Hey warehouse warriors and space savers! Feeling like your floor space is shrinking while your inventory keeps growing? You're not alone. One of the smartest moves in industrial and commercial storage is looking up. That's where mezzanine rack systems come into play. But with different types out there, how do you pick the right one? And more importantly, is shelling out the cash for a mezzanine rack truly worth it for your bottom line? Let's break it down, compare the main options, and see if this vertical leap makes financial sense.
The Vertical Solution: Why Consider a Mezzanine Rack?
Before diving into types, let's recap the why. A mezzanine rack is essentially a freestanding structural platform built within your existing building, creating a second (or even third!) level. Unlike traditional shelving, it leverages your unused vertical air space – space you're already paying rent or mortgage on. The primary goal? Dramatically increase your storage capacity or operational area without needing to move or build a costly addition.
Think about it: Instead of expanding your footprint outward (expensive and often impossible), you're building upward. This translates to storing more pallets, setting up dedicated packing stations, creating office space, or housing light assembly lines – all above your current floor. The core value proposition of any mezzanine rack is maximizing your cubic footage.
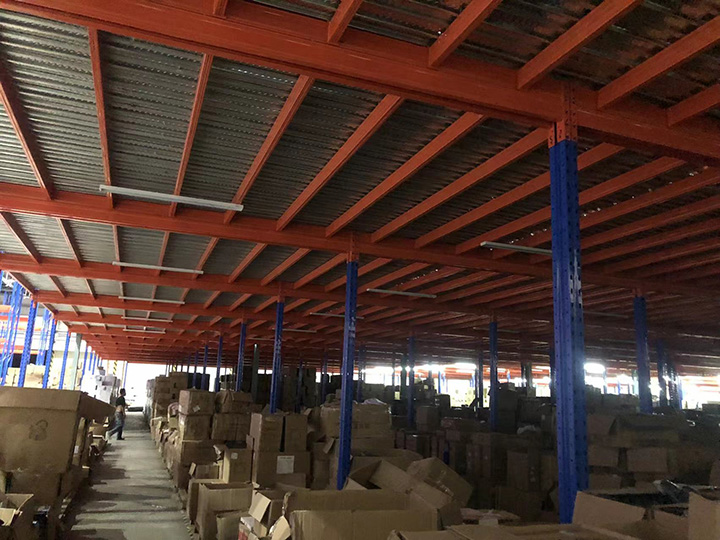
The Contenders: Breaking Down Major Mezzanine Rack Types
Not all mezzanine rack systems are created equal. Choosing the right one hinges on your specific needs: weight requirements, budget, flexibility, installation speed, and ceiling height. Here are the main players:
- Structural Steel Mezzanine Racks: The Heavy-Duty ChampionWhat it is: This is the classic, heavy-duty mezzanine rack. Built with robust steel columns, beams, and braces, it supports substantial loads. The decking is typically heavy-duty bar grating, checker plate, or concrete-filled metal deck.Pros: Unmatched strength and durability. Handles the heaviest pallet loads (often 1,000+ lbs per sq ft), machinery, or dense inventory. Offers the longest lifespan. Highly customizable in size and layout. Provides a very stable, permanent-feeling platform. Excellent fire rating potential.Cons: Highest upfront cost. Longer installation time due to welding/fabrication. Generally requires professional engineering and permitting. Less flexible if you need to reconfigure later. Can feel more "industrial."Best For: Warehouses storing heavy palletized goods, manufacturing plants needing machinery platforms, large distribution centers requiring maximum load capacity and permanence. If sheer strength and long-term stability are non-negotiable, this mezzanine rack is king.
- Bolt-Together (Shelf-Supported) Mezzanine Racks: The Flexible & Faster OptionWhat it is: This clever system integrates the mezzanine rack structure directly with heavy-duty pallet racking. The upright frames of the pallet racking act as the primary supports for the mezzanine deck above. Decking options include wire mesh, plywood, or light-duty steel panels.Pros: Significantly faster installation – often just bolted together. Lower upfront cost compared to structural steel. Offers good flexibility; the racking configuration underneath can often be adjusted, and the deck can potentially be relocated or expanded more easily. Utilizes the racking footprint efficiently.Cons: Lower weight capacity than structural steel (typically 250-500 lbs per sq ft). Height is constrained by the racking uprights. Decking might feel less solid underfoot than structural options. Requires very level floors for stability. Load capacity is tied to the racking configuration below.Best For: Warehouses needing additional storage levels primarily for palletized goods on racking, operations prioritizing speed of installation and lower initial investment, situations where moderate load capacity suffices. This mezzanine rack is ideal when racking is already planned or present underneath.
- Free-Standing Boltless Shelving Mezzanines: The Modular & Economical ChoiceWhat it is: Think super-sized boltless shelving units configured to create a platform. Built with heavy-duty vertical posts and beams that slot together without nuts and bolts, supporting a deck (usually particle board, steel panels, or wire mesh).Pros: Most economical upfront cost. Extremely modular and reconfigurable – you can disassemble, move, and resize sections relatively easily. Very fast installation. Good for lighter-duty applications.Cons: Lowest weight capacity among the main types (usually max 150-300 lbs per sq ft). Not suitable for heavy pallets or machinery. Decking can be less durable over time. May feel less stable than welded or bolted structures. Limited height potential.Best For: Retail stockrooms, light assembly areas, document storage archives, storing lighter boxes or bins, showroom displays, or situations requiring maximum flexibility and the lowest initial cost. This mezzanine rack shines for non-palletized, lighter inventory.
- Multi-Tier Rack Systems (Integrated Mezzanine Effect):What it is: While not always classified as a traditional "mezzanine," very tall pallet racking systems (like drive-in, push-back, or pallet flow) can effectively create multiple storage levels accessible from the floor, achieving a similar space-saving goal without a distinct, walkable deck across the entire area.Pros: Maximizes dense storage for specific SKUs. High cube utilization within the racking footprint. Often automated options available.Cons: Not a true walkable platform across a wide area. Access can be more complex (requires specific lift trucks). Less versatile for non-storage uses.Consider When: Pure high-density pallet storage is the sole objective, and a wide-open platform isn't needed.
Crunching the Numbers: Is a Mezzanine Rack Worth the Investment?
Okay, so you see the types. Now, the big question: Does the return justify the spend? Let's look at the factors:
- The Cost of NOT Doing It:Rent/Mortgage Savings: This is the BIG one. Adding 5,000 sq ft of usable space via a mezzanine rack inside your existing building is almost always cheaper per square foot than leasing or building 5,000 sq ft of new ground-level space, especially when you factor in land costs, construction time, property taxes, and potentially higher utility costs for a separate building.Operational Efficiency: Consolidating operations under one roof reduces travel time for staff and material handling equipment (saving labor and fuel/electricity). Faster order picking = happier customers.Avoiding Relocation Chaos: Moving an entire operation is incredibly disruptive and expensive. A mezzanine rack lets you grow in place.
- Upfront Investment Factors:Type Chosen: Structural steel costs more than bolt-together, which costs more than boltless shelving mezzanines.Size & Complexity: Obviously, bigger platforms and custom features (stairs, gates, conveyors, sprinklers, lighting) add cost.Decking Choice: Bar grating costs more than wire mesh.Engineering & Permits: Essential for structural steel and often for others, depending on local codes and size. Factor this in!Installation: Professional installation is recommended (often required) for safety and compliance.
- The ROI Calculation (Simplified):Think of it like this:Calculate Added Value: Determine the value of the new space. What would equivalent new space cost per month (rent/mortgage + taxes + insurance + estimated utilities)? Multiply by 12 for annual savings/value.Quantify Efficiency Gains: Estimate labor/time savings from consolidated operations. (e.g., reduced pick times, fewer forklift trips).Total Annual Benefit: Add #1 and #2.Total Project Cost: Include mezzanine rack materials, decking, engineering, permits, installation, stairs, safety features, lighting, sprinkler mods (if needed).Simple ROI: (Total Annual Benefit / Total Project Cost) x 100 = ROI Percentage. *Example: $50k annual savings / $100k project cost = 50% ROI in Year 1.*Payback Period: Total Project Cost / Total Annual Benefit = Years to recoup investment. *Example: $100k cost / $50k annual benefit = 2-year payback.*
Key Considerations Beyond Cost:
- Ceiling Height: You need ample clear height above the existing floor and above the planned mezzanine rack deck for safe clearance (people, equipment, sprinklers – OSHA requires min 7 ft 6 in headroom under sprinklers, often 18-24 inches below the roof deck).
- Floor Load Capacity: Your existing concrete slab must support the concentrated loads of the mezzanine rack columns, plus the live load (people, inventory, equipment) on the deck. A structural engineer is crucial here.
- Building Codes & Permits: This is non-negotiable. Mezzanine rack installations typically require permits and must comply with IBC (International Building Code), OSHA, fire codes (especially regarding egress paths, fire rating if separating spaces, sprinkler coverage), and local regulations. Don't skip this step!
- Safety Features: Guardrails, toe boards, secure stairs with handrails, proper gates, and adequate lighting are mandatory for any mezzanine rack. Factor these into the design and cost.
- Access: How will people and material handling equipment (like pallet jacks or small order pickers) get up there? Stairs are essential. Evaluate if a lift or conveyor is needed.
The Verdict: When Does a Mezzanine Rack Make Sense?
So, is it worth it? Generally, YES – if you have the vertical space and your core need is maximizing existing square footage cost-effectively. The investment in a mezzanine rack often pays for itself remarkably quickly, sometimes in just a few years, through avoided expansion costs and operational efficiencies.
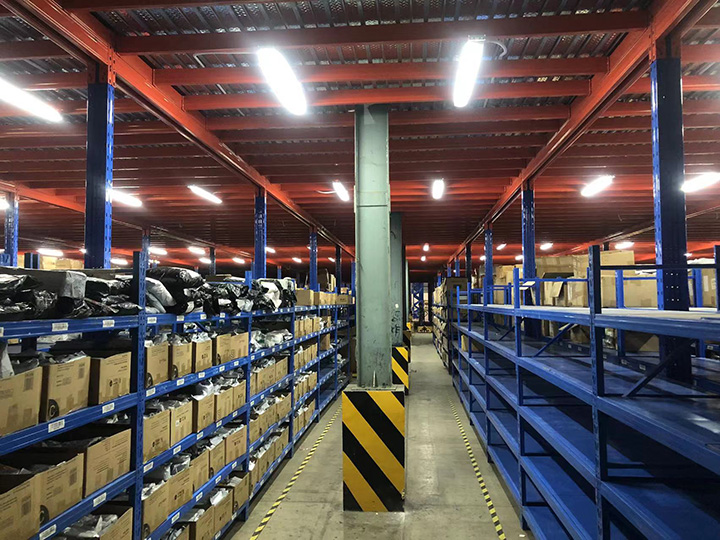
Specifically, it's a STRONG YES if:
- Your ceilings are high enough (typically 15 ft+ clear).
- Your floor slab can handle the load.
- You have predictable, long-term space needs.
- The cost of adding space vertically is significantly less than expanding outward or relocating.
- You choose the mezzanine rack type that perfectly matches your load requirements and budget (don't overbuy structural steel for light bins, don't underbuy boltless for heavy pallets!).
Proceed with Caution if:
- Your ceilings are too low.
- Your floor can't support the loads.
- Your space needs are very temporary or highly uncertain.
- Permitting hurdles are insurmountable or prohibitively expensive.
- You try to cut corners on safety or engineering.
Final Thoughts: Level Up Your Space
Investing in a mezzanine rack isn't just about buying steel and decking; it's about strategically unlocking the hidden potential of your building. By carefully comparing the structural steel, bolt-together (shelf-supported), and boltless shelving types, you can find the perfect fit for your weight needs, budget, and operational flow. Factor in all costs – materials, engineering, permits, installation, safety – and weigh them against the substantial savings of avoiding external expansion and the gains in operational efficiency.
For most businesses bursting at the seams, a well-chosen mezzanine rack system isn't just an expense; it's a high-return investment in productivity, efficiency, and future growth. Do your homework, get the engineering right, comply with the codes, and watch your usable space – and potentially your profits – soar. Time to build up!