Let's cut to the chase: warehouse space is expensive, and squeezing every drop of efficiency out of it is non-negotiable. You've probably heard whispers about drive-in racking – this dense storage beast promising to revolutionize how you store pallets. But is it just hype, or can it genuinely boost your bottom line? Buckle up, because we're diving deep into the real-world impact of drive-in racking on warehouse efficiency.
1. The Warehouse Squeeze: Why Efficiency Isn't Just Nice, It's Essential
Running a warehouse today feels like a constant puzzle. Rent keeps climbing. Labor is tight and pricey. Customers demand lightning-fast shipping. And your inventory? It seems to grow faster than you can find space for it. The pressure is on to:
- Store More Stuff: Maximize every single cubic foot of that expensive building.
- Cut Operating Costs: Reduce unnecessary travel time for forklifts and labor hours.
- Improve Inventory Control: Know where things are and access them reliably (even if not instantly).
- Optimize Flow: Make receiving, storing, picking, and shipping smoother.
Traditional selective racking (the kind where you can access every pallet directly) is fantastic for fast-moving SKUs. But what about that mountain of stuff that just… sits? The seasonal inventory, the raw materials, the cases of product you bought in bulk for a discount? That's where drive-in racking steps onto the scene.
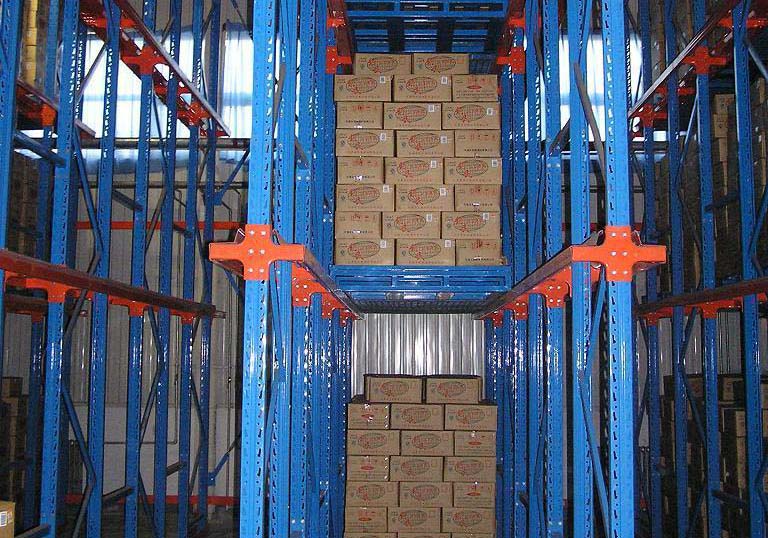
2. Drive-in Racking 101: How This Dense Storage Beast Works
Picture this: Instead of aisles separating every single rack row, drive-in racking creates deep lanes. Forklifts literally drive into these lanes to place or retrieve pallets. Think of it like multi-level parking for pallets, stacked several levels high.
Here’s the core setup:
- Deep Lanes: Pallets are stored on rails or rails, one behind the other, deep within the rack structure (often 5, 7, 10+ pallets deep per lane).
- Minimal Aisles: You only need aisles at the entrance to each lane, drastically reducing the total aisle space compared to selective racking.
- Support Structure: Robust uprights and horizontal beams support the load. Rails or beams guide the pallets within the lane.
- LIFO Principle: Last-In, First-Out. The last pallet loaded into a lane is the first one you can retrieve. You have to unload pallets from the front to access those behind them.
3. The Efficiency Payoff: Where Drive-in Racking Delivers (Big Time)
So, can drive-in racking actually increase efficiency? Absolutely – but specifically in the right scenarios. Here’s where it shines:
- Space Utilization Skyrockets (The #1 Benefit): This is the undisputed king of dense storage. By slashing the number of aisles, drive-in racking can typically increase your storage density by 40-75% compared to selective racking for the same footprint. If you're paying by the square foot, this translates directly to massive cost savings. More product stored in less space = major win.
- Reduced Infrastructure Costs: Storing more pallets in a smaller area means you potentially need a smaller building. That's huge savings on construction, heating, cooling, lighting, and property taxes. Even if you stay in your current space, you delay the need for costly expansion.
- Optimized for Slow-Moving, High-Quantity SKUs: Where drive-in racking truly boosts efficiency is for products with:Low turnover rates (long-term storage).High pallet quantities per SKU (you store many identical pallets).Products where batch control or LIFO inventory management is acceptable (like certain food items, chemicals with expiration dates, or raw materials).
- Lower Initial Investment (Per Pallet Position): While the racking structure itself is robust and can be costly upfront, the cost per pallet position stored is often significantly lower than selective racking because you're storing so much more in the same space.
- Protection for Stored Goods: Pallets are stored within the structure, offering some inherent protection from incidental forklift damage that can occur in open aisles. The rack structure itself also provides stability.
4. Reality Check: The Trade-offs of Drive-in Racking
It's not all sunshine and rainbows. Drive-in racking comes with inherent operational characteristics that impact efficiency differently than selective racking. Ignoring these is a recipe for frustration:
- LIFO Inventory Access: This is the big one. You cannot directly access any pallet you want, anytime. Retrieving a specific pallet buried deep often means moving several others out first. This significantly slows down access compared to selective racking. It’s efficient on space, less so on access speed for specific pallets.
- Reduced Throughput Speed: Loading and unloading lanes takes more time and careful maneuvering than grabbing a pallet from a selective rack. Forklift operators need specific training.
- Potential for Product Damage: While offering some protection, the close quarters within a lane and the need to push/pull pallets on rails increases the potential for product damage if not handled carefully or if pallets are unstable.
- Lower Selectivity: You have less flexibility to pick individual SKUs or small quantities directly from the rack. It’s primarily designed for full-pallet in/full-pallet out.
- Higher Forklift Operator Skill Requirement: Navigating deep lanes safely and efficiently requires skilled, trained operators.
5. Drive-in Racking vs. The Alternatives: Picking the Right Tool
Is drive-in racking the only dense storage option? Nope. Let’s compare:
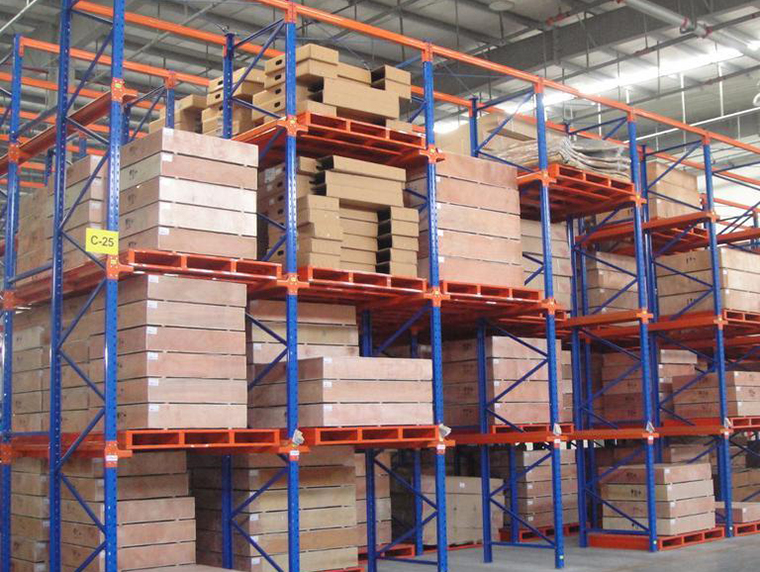
6. Making Drive-in Racking Work FOR Your Efficiency: Implementation Tips
So, you think drive-in racking might be the answer? Maximize its efficiency impact with smart implementation:
- SKU Profiling is KING: Rigorously analyze your inventory. Drive-in racking should ONLY be used for truly slow-moving SKUs with high pallet quantities per SKU. Don't put your fast-movers here!
- Lane Depth Matters: Don't just build lanes as deep as possible. Balance density with practicality. Deeper lanes mean longer retrieval times for the back pallets. Analyze your typical withdrawal quantities per SKU.
- Invest in Quality & Professional Design: This is heavy-duty storage. Use reputable suppliers and ensure the design is engineered for your specific loads, building, and seismic requirements. Don't cut corners.
- Prioritize Operator Training: Comprehensive training on safe lane entry/exit, proper pallet placement/retrieval, and awareness of the LIFO constraint is crucial for safety and operational efficiency.
- Robust Warehouse Management System (WMS): Your WMS must accurately track exactly which pallet (by lot, date, etc.) is in which position within each drive-in racking lane. This is non-negotiable for inventory accuracy and efficient retrieval planning.
- Strategic Placement: Locate your drive-in racking areas away from high-traffic picking zones. Think of it as your "deep storage" or "bulk reserve" area.
- Consider Selective Access Ends: For some setups, having one selective-accessible bay at the end of a drive-in racking block can offer slightly more flexibility for a key SKU.
7. When Drive-in Racking Might NOT Be Your Efficiency Hero
Let's be brutally honest: Drive-in racking is a specialized tool. It won't increase efficiency, and will likely tank it, if:
- You Need High Selectivity/Fast Access to Many SKUs: If you're constantly picking individual cases or various SKUs, selective or carton flow is far better.
- Your Inventory Turns Over Quickly (FIFO Critical): If items expire or need strict rotation (like fresh produce), FIFO systems like pallet flow are essential.
- You Have Low Quantities per SKU: Storing only 1-2 pallets per SKU in a deep lane is incredibly inefficient use of the lane.
- Forklift Traffic is Intense: Adding complex drive-in racking maneuvers to a chaotic, high-traffic warehouse can create bottlenecks and safety hazards.
- Pallets are Unstable or Non-Standard: Drive-in racking relies on stable pallets moving smoothly on rails. Poor-quality pallets are a recipe for jams and damage.
The Verdict: Yes, Drive-in Racking CAN Boost Efficiency – But Only If You Play By Its Rules
So, can drive-in racking increase your warehouse efficiency? The resounding answer is YES – but with a massive asterisk. Its superpower is unmatched storage density for slow-moving, high-quantity-per-SKU inventory. If you have acres of pallets of the same thing just sitting there (think: seasonal goods, raw materials reserves, archival stock, promotional overstock), drive-in racking is arguably the most cost-effective way to reclaim vast amounts of floor space and slash your per-pallet storage costs. This directly translates to tangible efficiency gains on your real estate and infrastructure costs.
However, it sacrifices speed of access and selectivity. Trying to use it for fast-moving items, items needing FIFO, or SKUs with low pallet counts will destroy any potential efficiency gains and create operational nightmares.
The bottom line? Drive-in racking isn't magic. It's a powerful, specialized tool. Implement it strategically for the right inventory profile, with excellent design, training, and WMS support, and it becomes a powerhouse for maximizing space utilization and reducing core storage costs – key pillars of warehouse efficiency. Force it into the wrong application, and it becomes an expensive, frustrating obstacle. Know your inventory, understand the trade-offs, and deploy drive-in racking where its strengths deliver maximum impact. That's how you turn dense storage into real efficiency wins.