Alright, let's talk about a constant headache in the warehousing world: running out of space. You're staring at your facility, racks climbing towards the ceiling, aisles getting tighter, and you know you're not using that cubic footage as efficiently as possible. If you're hitting that wall (literally and figuratively), and pallet selectivity isn't your top priority for every single SKU, then Drive-in Racking deserves a long, hard look. It might just be the high-density powerhouse you've been searching for.
The Space Crunch: Feeling the Squeeze?
We've all been there. Business is good (great, even!), inventory levels are rising to meet demand, but your existing storage setup is groaning under the pressure. Traditional selective pallet racking, while versatile, dedicates a massive chunk of your floor plan to those access aisles. Every aisle is essentially "wasted" space – space that could be holding valuable product. You find yourself:
- Contemplating expensive expansion: Building out or moving is a huge capital investment and a major operational disruption.
- Dealing with overflow chaos: Pallets stacked on the floor? That’s a safety hazard, an efficiency killer, and an inventory nightmare.
- Facing slower operations: More aisles mean longer travel times for your forklifts, burning fuel and operator hours.
If this sounds familiar, it's time to explore solutions designed specifically for maximizing storage density. That's where Drive-in Racking shines.
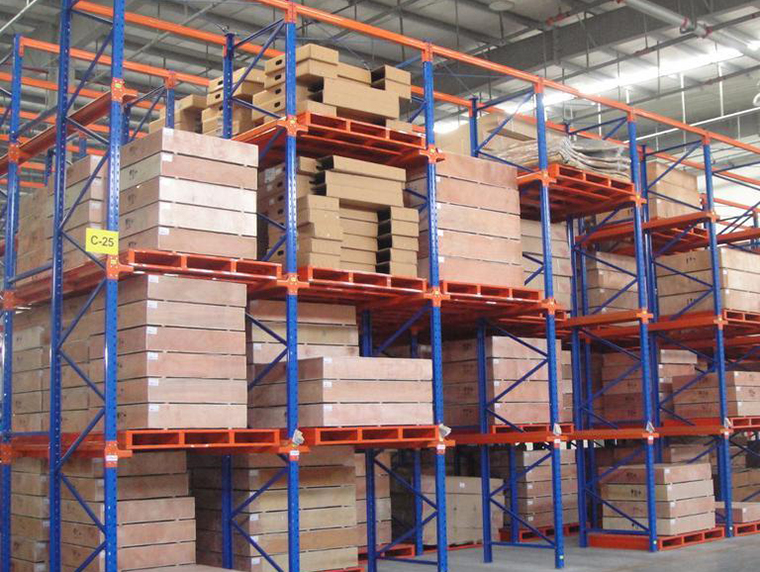
Drive-in Racking 101: What Exactly Is It?
Think of Drive-in Racking as a high-density storage system where your forklift literally drives into the rack structure itself. Unlike selective racks where you access each pallet from an aisle, Drive-in Racking stores pallets on rails or rails and beams multiple deep within a single lane. Pallets are stored one behind the other, on the same level.
Here's the core principle: Last-In, First-Out (LIFO) inventory management. The last pallet loaded into a lane is the first one retrieved. This makes it ideal for storing large quantities of the same product (SKU) with high turnover, or for products with long shelf lives where batch rotation is less critical.
Key Components of a Drive-in Racking System:
- Vertical Frames: These form the upright structure at the ends of each lane and often along the back. They need to be robust to handle the impacts from forklifts entering and exiting.
- Guide Rails: Installed along the length of the lane, both at floor level and higher up, these guide the forklift wheels and support the pallets. They define the lane path.
- Beams (Optional in some designs): Some systems use beams perpendicular to the rails at each storage level to provide additional support, while others rely solely on the longitudinal rails.
- Entry Guides: Critical safety and guidance components at the entrance of each lane, helping the forklift operator enter smoothly and accurately.
- Bracing & Ties: Essential for overall structural integrity, connecting frames and stabilizing the entire system, especially important given the dynamic forces of forklifts operating within the structure.
Why Drive-in Racking is a Space Maximizing Game-Changer: The Core Benefits
So, what makes Drive-in Racking such a compelling option when space is premium? Let's break down the advantages:
- Unbeatable Storage Density: This is the headline act. By eliminating numerous access aisles found in selective racking, Drive-in Racking can increase your storage capacity by up to 75% or more within the same floor area. You store pallets deep, utilizing virtually the entire width and height of your building footprint. More pallets per square foot = maximized space.
- Optimized Cube Utilization: Drive-in Racking isn't just about floor space; it excels at utilizing your building's vertical cube right up to the allowable safe height. You get maximum pallet positions from floor to ceiling within each deep lane.
- Reduced Aisle Requirements: Instead of an aisle for every single rack row, you only need one access aisle per bay of Drive-in Racking lanes (typically 2-10 lanes deep). This drastic reduction in aisle space is where the density magic happens.
- Lower Cost per Pallet Position: While the initial investment per foot of Drive-in Racking might be higher than selective racking, the cost per pallet position is usually significantly lower because you're storing so many more pallets in the same overall space. It's a smarter capital allocation for high-volume storage.
- Improved Handling Efficiency for Bulk Storage: When storing large quantities of a single SKU, operators can quickly load or unload an entire lane without needing to navigate multiple aisles. Loading a full lane is often faster than placing pallets individually across many selective positions.
- Enhanced Product Protection (For Suitable Goods): Pallets stored deep within a Drive-in Racking lane are less exposed to potential damage from forklifts operating in main aisles compared to pallets sticking out on selective racks.
Is Drive-in Racking Right For YOUR Operation? Key Considerations
Drive-in Racking is powerful, but it's not a universal solution. It excels in specific scenarios. Ask yourself:
- Inventory Profile: Do you have large quantities of the same SKU? Drive-in Racking thrives on homogeneity within each lane. Mixing SKUs in a lane leads to inefficiency and potential errors.
- Inventory Turnover & Rotation: Does LIFO (Last-In, First-Out) work for your products? It's perfect for non-perishable bulk goods, raw materials, or finished goods with long shelf lives. It's not suitable for strict FIFO (First-In, First-Out) requirements or highly perishable items unless managed very carefully (e.g., dedicated lanes per batch).
- Forklift Requirements: Operating within Drive-in Racking demands skilled operators and the right equipment – typically reach trucks or counterbalanced forklifts specifically configured for narrow aisle or drive-in operation. Maneuvering within the confined lane requires precision and training. Dedicated "drive-in" forklifts are often used.
- Selectivity Sacrifice: This is the trade-off. You cannot directly access any pallet except the one at the front of the lane. If you need frequent access to multiple different SKUs simultaneously, selective racking remains superior for those items.
- Throughput Speed: While loading/unloading a full lane can be fast, retrieving a pallet from the back of a full lane requires moving all the pallets in front of it first. This makes it less ideal for extremely high-speed, random access operations.
Best Use Cases for Drive-in Racking:
- Bulk Storage of Single SKUs: Think beverages, packaging materials, paper products, building supplies, seasonal items (off-season storage).
- Cold Storage Facilities: Where space is incredibly expensive, maximizing density is paramount. Drive-in Racking is very common in freezers and coolers.
- Raw Material Warehousing: Storing large quantities of uniform raw materials used in production.
- Finished Goods Buffer Storage: Holding large volumes of a specific finished product before shipment.
- Archiving & Low-Access Inventory: Storing items that are shipped infrequently but in bulk when needed.
Implementing Drive-in Racking: Getting it Right
Jumping into Drive-in Racking requires careful planning:
- Thorough Needs Analysis: Audit your inventory – SKU velocity, cube size, quantities, turnover patterns. Identify which products are true bulk candidates for Drive-in Racking.
- Expert Design & Engineering: This is crucial. Work with reputable racking manufacturers and engineers. They'll calculate loads, design lane depths, specify rail/beam configurations, ensure proper clearances, and verify structural integrity for your specific building and forklifts. Don't cut corners here!
- Site Preparation: Floor flatness is critical for smooth forklift operation within the lanes. Reinforcement might be needed, especially for heavier loads or taller systems. Ensure adequate lighting within the lanes.
- Vetting Installation Teams: Choose experienced installers familiar with the complexities and safety requirements of Drive-in Racking systems.
- Operator Training is Non-Negotiable: Driving into rack structures requires specialized skills. Invest in comprehensive training focusing on safe entry/exit, precise load handling within the confined space, speed control, and understanding load limits/lane capacities. Refresher training is essential.
- Rigorous Safety Protocols: Implement strict rules: speed limits within lanes, clear signage, mandatory seatbelt use, regular inspections of rails and entry guides for damage. Consider lane occupancy signals if multiple lanes share an access aisle.
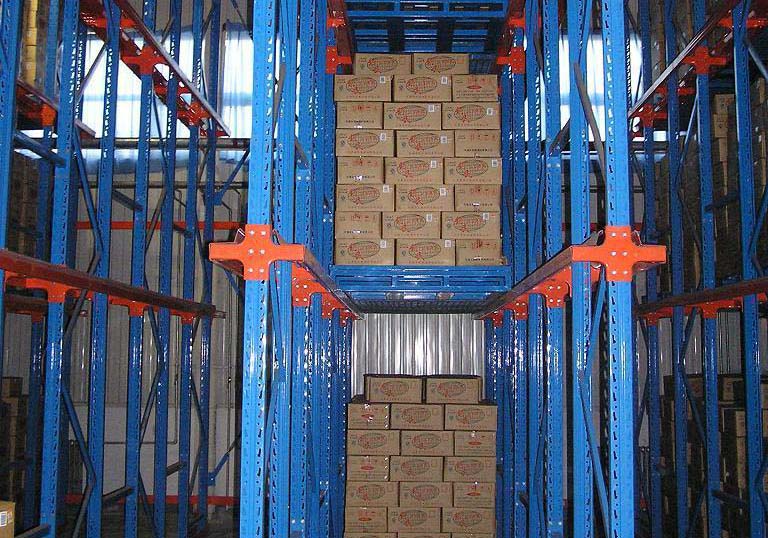
Beyond the Basics: Drive-in Racking Innovations
The world of Drive-in Racking isn't static. Innovations are enhancing safety and efficiency:
- Enhanced Safety Systems: Proximity sensors, lane occupancy lights, and improved impact-resistant entry guides are becoming more common.
- Hybrid Systems: Combining Drive-in Racking for bulk items with selective racking or other systems (like pallet flow) for faster-moving or multi-SKU items in the same warehouse.
- Improved Rail Designs: Designs offering smoother operation and better durability against impacts.
- Integration with WMS: Warehouse Management Systems can help track which specific pallet is at the front of which lane, improving inventory visibility even within the LIFO structure.
The Verdict: Unlock Your Warehouse's True Potential
If you're genuinely looking to maximize your warehouse space and you have significant volumes of homogeneous product, Drive-in Racking is far more than just an "option" – it's often the most efficient and cost-effective solution. The dramatic increase in storage density directly translates to deferred expansion costs, lower real estate expenses per pallet stored, and a more streamlined operation for your bulk goods.
Yes, it requires careful implementation, skilled operators, and a commitment to safety. The LIFO principle is a key factor to embrace. But when the fit is right, the payoff in terms of space utilization and operational efficiency for bulk storage is undeniable.
Don't just squeeze more in chaotically. Think strategically. Consider Drive-in Racking. It might be the high-density key that unlocks your warehouse's true capacity and sets your operation up for scalable growth. Get a qualified racking specialist to assess your specific needs and crunch the numbers – the potential savings and efficiency gains could be substantial.