Choosing the right Pallet Racking size isn't just about fitting stuff in your warehouse – it's about maximizing your space, boosting efficiency, keeping everyone safe, and saving serious money. Get it wrong, and you're looking at wasted space, frustrated forklift drivers, damaged goods, and potential safety hazards. Get it right, and your operation hums. So, let's break down exactly how to figure out what size Pallet Racking system you really need.
1. The Starting Point: Know Your Loads Inside and Out
Before you even glance at racking specs, you gotta become best friends with your pallets and what sits on them. This is foundational:
- Pallet Dimensions (L x W): Measure your actual pallets – not just the "standard" size you think you use. Common US pallets are 48"x40" (GMA), but 42"x42", 48"x48", and others exist. Measure several to account for slight variations. Don't forget overhanging loads!
- Pallet Height: How tall is the pallet itself? Add the height of the typical load sitting on it. This gives you your unit load height.
- Unit Load Weight: This is critical for structural integrity. What's the maximum weight any single pallet load will ever be? Be realistic, but account for peak weights. Pallet Racking is rated for specific capacities – exceeding this is dangerous.
- Load Stability: Are your loads stable cubes, or are they irregular, top-heavy, or prone to shifting? This influences the type of Pallet Racking (e.g., wire decking might be needed) and potentially the required beam capacity for uneven weight distribution.
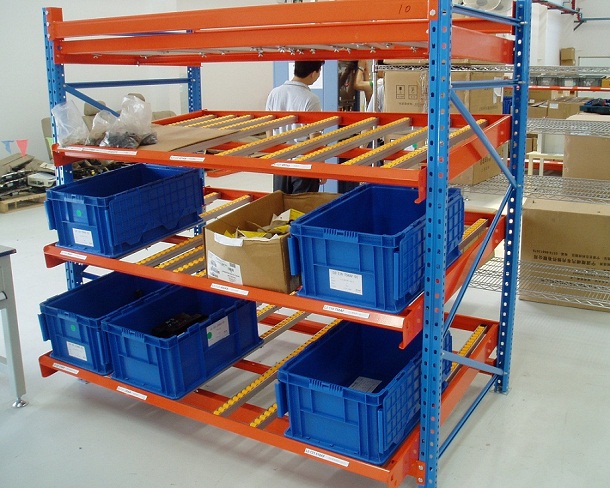
2. How Tall Can You Go? Vertical Space is Prime Real Estate
Warehouse height is your most valuable asset. Utilizing it effectively is key to storage density.
- Clear Ceiling Height: Measure from the finished floor to the absolute lowest overhead obstruction (lights, sprinklers, HVAC ducts, structural beams). Don't guess – get up there with a tape measure!
- Forklift Capability: What's the maximum lifting height of your forklifts or narrow-aisle equipment when fully extended? Your Pallet Racking height is limited by both your ceiling and your equipment's reach. Factor in safe operating clearances.
- Required Clearances: OSHA mandates minimum clearances:6-inch Rule: You need at least 6 inches of vertical space between the top of a stored pallet and the bottom of the beam above it. This allows for safe placement/removal and accounts for pallet deflection.Sprinkler Clearance: NFPA 13 requires specific clearances (usually 18-36 inches) below sprinkler heads. Never block sprinklers!Lighting/Airflow: Don't rack right up to lights or vents; maintain access and airflow.
- Calculating Frame Height: Start with your clear ceiling height. Subtract: Sprinkler clearance, Lighting clearance, Beam height (typically 6-8 inches), the 6-inch load clearance, and your unit load height. The result is your potential upright frame height per level. You'll typically have multiple beam levels.
3. How Deep Should Your Racking Be? Balancing Access and Stability
Depth impacts how easily you can access pallets and how stable the load is on the beam.
- Pallet Depth + Overhang: Your beams need to support the entire pallet depth plus any product overhang. Standard rule of thumb: Beams should be at least 3 inches longer than the pallet depth on each end (so 6 inches total longer). For a 48" deep pallet, you'd want minimum 54" long beams. Many opt for 60" or 66" beams for 48" pallets for extra safety and stability, especially with unstable loads. Never let the pallet overhang the beam support!
- Frame Depth: This is the front-to-back dimension of the upright frames. Common depths are 42", 48", 54", 60". The frame depth needs to accommodate your beam length plus the required end connectors. Your racking supplier will match compatible beams and frames.
- Drive-In/Drive-Thru Racking: If considering these dense systems, depth is defined by the number of pallets stored deep and the clearances needed for equipment maneuvering within the lane.
4. Getting the Width Right: Aisles Dictate Everything
The width of your aisles is arguably the most critical factor determining your overall storage density and the type of equipment you need.
- Forklift Type is King:Conventional Forklifts (Counterbalance): Need wide aisles (typically 11-13 feet+). Requires wider aisles to maneuver and turn.Narrow Aisle (NA) Forklifts: Can operate in aisles 8-10 feet wide. Use specialized guidance systems.Very Narrow Aisle (VNA) Forklifts: Operate in aisles 6 feet or less. Require exceptional floor flatness and often wire or rail guidance.
- Calculating Aisle Width: It's not just the truck width! You must add:Pallet width (or length, depending on orientation)Clearance on each side of the pallet (usually 3-6 inches minimum for safe maneuvering)Clearance for the forklift mast/tires from the racking uprights (another 3-6 inches)
- Pallet Orientation: Are pallets placed in the racking with the 48" side facing the aisle (short side facing out) or the 40" side (long side facing out)? This impacts the "width" dimension the aisle needs to accommodate. Short-side facing out is most common as it requires less beam length for a given pallet depth.
- Impact on Storage Density: Narrower aisles = more rows of Pallet Racking = higher density. But you need the right equipment to navigate them safely.
5. Beam Length and Level Spacing: Fine-Tuning for Your Loads
This is where your Pallet Racking gets customized to your specific inventory.
- Beam Length: As covered in depth, determined by pallet depth + overhang + safety margin. Standard lengths are 96", 102", 108", 120", 144" etc.
- Vertical Level Spacing: This determines how many pallets you can stack vertically in a single bay.Formula: Unit Load Height + 6-inch Clearance (minimum) + Beam Height = Space needed per level.Example: Load Height = 50", Beam Height = 6", Clearance = 6". Space per level = 62". If your clear height to obstructions allows 300", you could potentially fit 300 / 62 ≈ 4.8 levels. So, 4 levels is practical (4 x 62" = 248" used), leaving space for top clearance. Always round down for safety.Adjustability: Most Pallet Racking systems use clip-in beams, allowing you to easily adjust level heights as your inventory profile changes. This flexibility is a major benefit.Varying Load Heights: If you store different height loads, you might set different level spacings within the same bay or section. Plan your layout accordingly.
6. The Non-Negotiables: Safety Standards (OSHA & ANSI MH16.1)
Ignoring safety when sizing Pallet Racking is asking for trouble. Compliance is mandatory.
- Load Capacity: Every component (upright frame, beam, connector, deck) has a rated capacity. Your heaviest anticipated unit load must be less than the lowest rated capacity of any component in its support structure. Never exceed ratings! Load signs are required.
- Column Guards: Upright frames exposed to potential forklift impact (especially at aisle ends and corners) MUST be protected by substantial column guards (bollards).
- Load Beams Securely Seated: Ensure beams are fully seated and secured with the manufacturer's locking clips. Bent or damaged beams must be replaced immediately.
- Proper Decking: If using decking (wire mesh, plywood, steel), it must be correctly supported by the beams and rated for the intended load. Don't overload decking.
- Regular Inspections: Implement a documented inspection program per OSHA guidelines. Look for damage (bends, cracks, missing clips) and ensure loads are within capacity and properly placed.
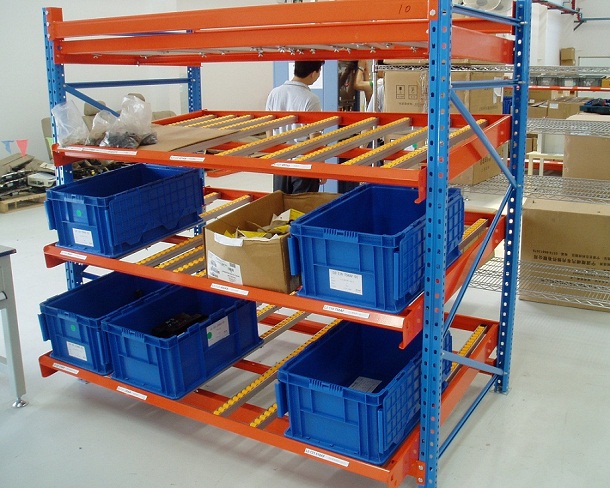
7. Common Sizing Mistakes to Avoid (Save Yourself the Headache!)
- Ignoring Actual Pallets & Loads: Assuming "standard" sizes and weights.
- Forgetting Clearances: Especially the 6-inch rule and sprinkler clearance.
- Mismatching Equipment & Aisles: Buying VNA racks but only having counterbalance forklifts.
- Overlooking Weight: Focusing only on dimensions, not load weight and stability.
- Neglecting Future Needs: Sizing only for today's inventory, not allowing for growth or product changes.
- DIY Engineering: Pallet Racking is structural. Always work with a reputable supplier who provides engineered layout drawings and calculations stamped by a Registered Professional Engineer (RPE). This is often required by code and your insurer.
Putting It All Together: Finding Your "Sweet Spot"
Choosing the right Pallet Racking size isn't about finding one magic number; it's about balancing multiple factors:
- Your Loads: Dimensions, Weight, Stability.
- Your Building: Clear Height, Obstructions, Floor Condition.
- Your Equipment: Forklift Type & Capabilities.
- Safety & Compliance: OSHA, ANSI, Fire Codes.
- Your Budget: Upfront cost vs. long-term ROI (density, efficiency, safety).
- Future Flexibility: Adjustable systems are worth the investment.
The Smartest Move: Consult the Pros
While understanding these factors is crucial, sizing Pallet Racking for a complex warehouse is best done with expert help. Reputable Pallet Racking suppliers offer:
- On-Site Surveys: Experts measure your space, assess loads, and understand your workflow.
- Engineered Layouts: CAD drawings showing optimized rack placement, sizes, capacities, and aisle widths.
- Load Calculations: Ensuring all components meet or exceed your requirements.
- Equipment Recommendations: Matching the rack system to your MHE.
- Code Compliance: Ensuring designs meet OSHA, ANSI, and local regulations.
Questions to Ask Your Pallet Racking Supplier:
- "Can you provide engineered drawings stamped by an RPE?"
- "What are the exact load capacities for the frames and beams you're proposing?"
- "How does this layout optimize my storage density for my specific inventory and equipment?"
- "What safety features (column guards, rack protectors) are included?"
- "What are my options for adjustability and future reconfiguration?"
Conclusion: Size Matters – Get It Right
Investing time and effort into accurately determining the size of Pallet Racking you need pays massive dividends. It unlocks your warehouse's potential, streamlines operations, protects your people and inventory, and delivers a strong return on investment. Don't gamble with guesswork. Understand your requirements, prioritize safety, and partner with experienced professionals to design and install a Pallet Racking system that fits your operation perfectly – today and as you grow. Ready to maximize your space? Get that expert consultation scheduled!