Hey warehouse warriors and logistics leaders. Let's cut to the chase: space is money. And if you're still running single-deep pallet racking in a market demanding razor-thin margins and hyper-efficiency, you might be literally leaving dollars on the floor. Double-deep-pallet-racking isn't just some niche storage fad; it's a legit game-changer for operations needing serious density without the sky-high price tag of automated systems. Here’s why you should seriously think about making the switch – like, today.
1. The Space Squeeze is Real (And Costing You Big Bucks)
Picture your current setup. Aisles wide enough for a forklift to comfortably turn, with single rows of pallets facing out. Standard stuff, right? But look closer. All that precious square footage eaten up by aisles? That's pure, expensive overhead – rent, utilities, taxes. Every unused cubic foot is burning a hole in your P&L.
- The Density Difference: Double-deep-pallet-racking tackles this head-on. By storing pallets two deep instead of one, you effectively slash the number of aisles needed by nearly half. Think about it: two pallets deep per bay means you're storing way more product in the same footprint. We're talking potential storage increases of 40-50% compared to single-deep setups. That translates directly to lower cost per pallet position.
- The Bottom Line Impact: More pallets per square foot = better utilization of your expensive warehouse real estate. For growing businesses bursting at the seams, double-deep-pallet-racking can often delay or even eliminate the need for costly facility expansions or relocations. It turns wasted aisle space into profitable storage space.
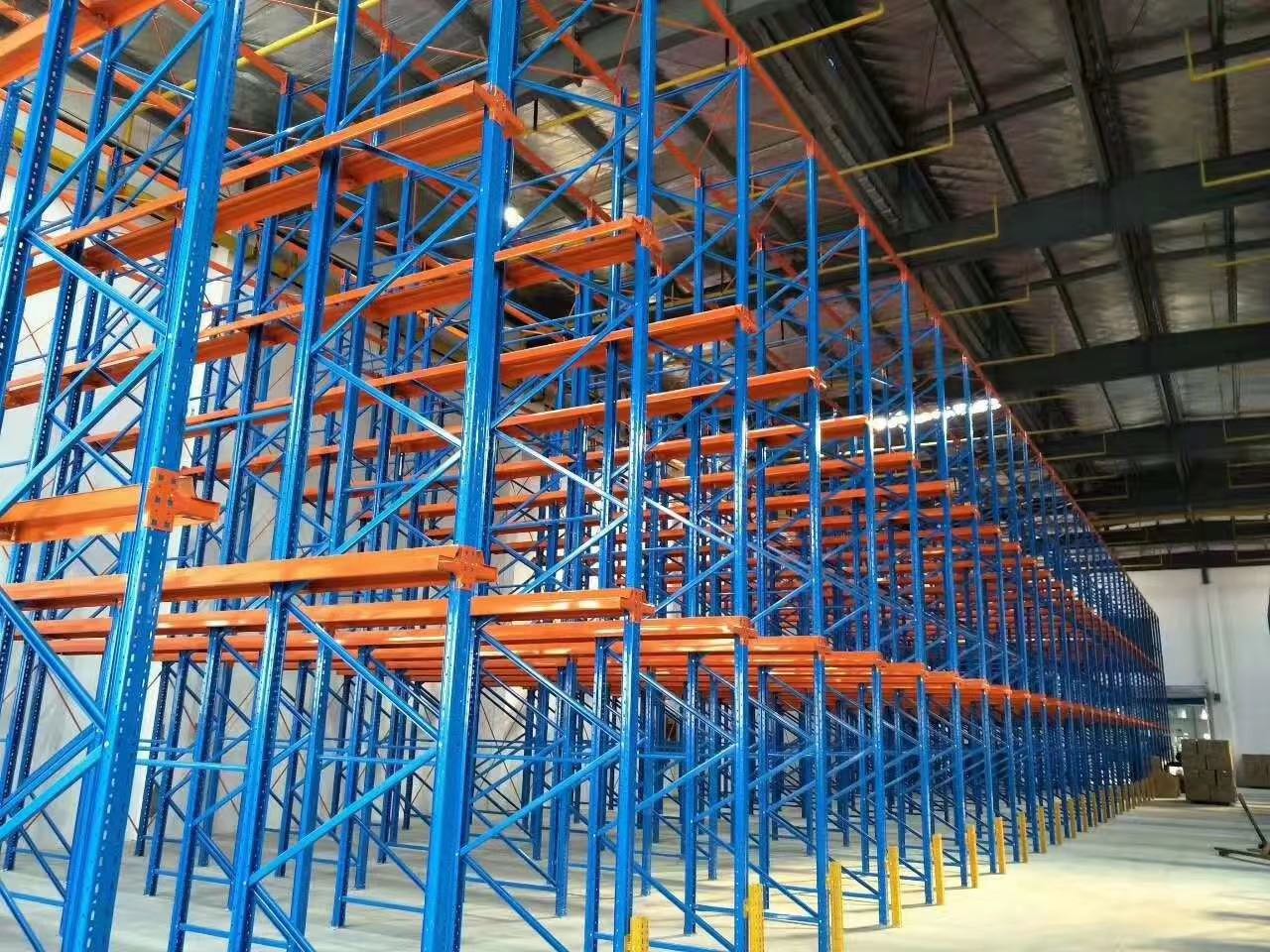
2. It’s the Sweet Spot Between Cost and Complexity
Okay, automated storage and retrieval systems (AS/RS) are cool. Super dense, super fast. But let's be real – they come with super-sized price tags and complexity. If you're not Amazon-sized, that investment might be out of reach. On the flip side, single-deep is simple but inefficient.
- The Goldilocks Solution: Double-deep-pallet-racking hits that "just right" zone. It offers a massive jump in density over single-deep (way more than drive-in or push-back racks for many SKUs) without the astronomical cost and IT integration headaches of full automation. It leverages your existing forklift assets (with one crucial upgrade – more on that soon) and standard pallet handling processes, just smarter.
- Faster ROI: The upgrade path is clearer. The capital expenditure is significantly lower than automation. This means you see a tangible return on your investment much faster through reduced operational costs per pallet and deferred expansion costs. It's a practical, scalable solution for smart businesses.
3. Making Your Forklift Fleet Work Smarter (Not Harder)
Yes, moving to double-deep-pallet-racking requires the right equipment. You absolutely need reach trucks with deep-reach capability. Standard counterbalance forklifts won't cut it. But hear me out – this isn't a drawback; it's an optimization.
- Deep-Reach Reach Trucks: These are the workhorses for double-deep-pallet-racking. Their telescoping forks extend deep into the racking to safely place and retrieve the second pallet. Operators stay safely on the ground, maneuvering in narrower aisles. If you already use reach trucks for single-deep, the transition is smoother.
- Narrower Aisles = More Space: Because you're storing pallets two deep, you can actually design narrower aisles compared to single-deep layouts needing wider turning radii. Reach trucks excel in these narrower aisles (think 10-11 feet wide vs. 12-13+ feet for counterbalance in single-deep). This aisle reduction further contributes to your overall space savings.
- Operator Skill Matters: Good training is non-negotiable. Operators need to be precise placing and retrieving that second pallet. But the efficiency gains from reduced travel distances (fewer aisles!) often mean overall productivity increases once the team is up to speed.
4. Optimizing Your Inventory Like a Pro
Double-deep-pallet-racking isn't just about cramming more in; it forces smarter inventory management – a good thing!
- Perfect for High-Volume, Fewer SKUs: This system shines brightest when you have solid quantities of fewer SKUs. Think high-turnover items, bulk storage, or cases where you dedicate a lane to a single SKU stored two pallets deep. It minimizes the need for constant lane switching.
- The FIFO Factor: Unlike drive-in racking, double-deep-pallet-racking inherently supports First-In-First-Out (FIFO) inventory rotation within each lane. You load one side and unload from the other. This is crucial for perishables, items with expiration dates, or anything where stock rotation is essential.
- Slotting Strategy is Key: Careful planning is vital. Group high-volume SKUs together in dedicated double-deep lanes. Avoid mixing slow and fast movers in the same lane to prevent the dreaded "blocked pallet" scenario (where the front pallet isn't the one you need next). Good Warehouse Management System (WMS) integration is a huge plus for directing put-away and retrieval efficiently.
5. Busting the Myths: Safety, Access & Cost Concerns
Let's address the elephants in the warehouse:
- "Isn't it less safe?" Properly installed double-deep-pallet-racking is just as safe as any other system when used correctly. Key factors:Quality Equipment: Use racks rated for the load and installed by professionals.Trained Operators: Skilled operators with deep-reach trucks are essential.Load Integrity: Pallets must be stable and undamaged. Front pallets blocking access to rear pallets must be moved carefully.Selective Access: Yes, the rear pallet isn't instantly accessible if a different SKU is in front. This is why SKU discipline and slotting are critical. It's a trade-off for density, managed by good processes.
- "Won't my throughput slow down?" Potentially, for retrieving a specific rear pallet blocked by a front one. However, the significant reduction in travel time due to fewer aisles and shorter distances often leads to a net gain in overall productivity, especially for full-pallet movements of high-volume SKUs.
- "The forklift upgrade cost is too high!" Factor in the total picture. The savings from increased storage density (delaying expansion, lower cost per pallet position) and potential productivity gains often quickly offset the cost of acquiring or leasing deep-reach reach trucks. Leasing options can also ease the initial capital burden.
6. Is Double Deep Pallet Racking Right For YOUR Operation?
It's not a magic bullet for everyone. Consider this checklist:
- YES, if...You are seriously space-constrained and need immediate density gains.You have high-volume SKUs with solid inventory turns.You primarily handle full pallet loads (less than ideal for intense case picking).You're willing to invest in deep-reach reach trucks and operator training.You have (or can implement) solid inventory control/WMS practices.
- Maybe NOT, if...Your operation is 100% focused on fast, single-item or case picking (selective racking or carton flow might be better).You have thousands of very slow-moving SKUs where every pallet needs instant, random access.You cannot justify the investment in deep-reach forklifts.Your pallet quality/load stability is consistently poor.
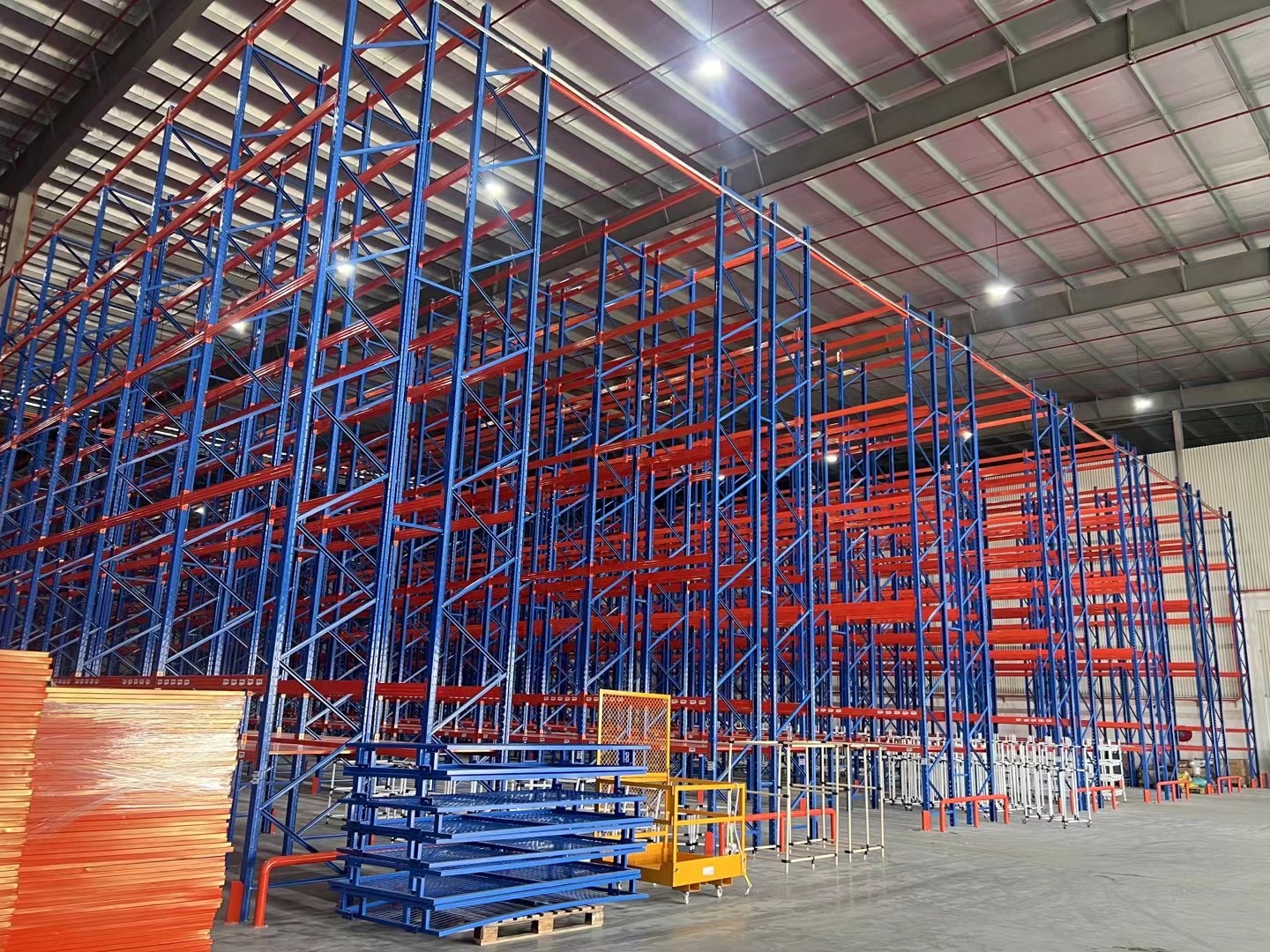
7. Making the Move: Practical Next Steps
Convinced double-deep-pallet-racking could be your density hero? Here's how to start smart:
- Audit Your Inventory: Analyze your SKU velocity. Identify the high-volume candidates perfect for double-deep lanes.
- Consult the Pros: Engage a reputable racking manufacturer and a qualified warehouse layout consultant. They'll assess your space, needs, and feasibility.
- Forklift Check: Talk to your forklift dealer. Demo deep-reach reach trucks. Factor in acquisition/leasing costs.
- Plan the Layout: Design the racking configuration, aisle widths, and lane assignments meticulously. Integrate with your WMS if possible.
- Train Your Team: Invest heavily in comprehensive operator training focused on safety and precision handling in the double-deep environment.
- Phase It In: Consider a pilot area before a full warehouse overhaul. Test, refine, and then scale.
The Bottom Line: Density, Dollars, and Doing More With What You Have
The pressure on warehouses and DCs is relentless. Double-deep-pallet-racking offers a powerful, proven, and practical solution to the universal challenge of space. It dramatically increases storage capacity, slashes your real estate cost per pallet, and boosts operational efficiency – all without breaking the bank on futuristic automation.
If you're staring down rising costs, overflowing inventory, or the daunting prospect of moving to a bigger building, hitting pause and evaluating double-deep-pallet-racking isn't just smart; it might be the most strategic logistics decision you make this year. It’s time to look beyond single-deep and reach deeper into your storage potential. Stop letting valuable space go to waste – explore how double-deep can transform your operation today.