Alright, let’s talk real warehouse problems. You’re staring at your space, inventory’s piling up, and you need more – more storage, more efficiency, more room to breathe. The classic move? Slap up some heavy-duty shelving. But hold on, there’s another player in the game that might just be your space-saving superhero: the Warehouse Mezzanines Floor. So, which one wins? Shelving or Warehouse Mezzanines Floor? Buckle up, because the answer is a classic consultant cop-out: it depends on your specific hustle. Let’s break it down.
Round 1: The Space Race – Vertical vs. Horizontal
- Regular Shelving (The Horizontal Warrior): Shelving is all about maximizing your existing floorplate. You go taller with narrow-aisle setups or very high bay racks. It’s fantastic for dense storage of palletized goods or bins. You pack it in tight, aisle space is minimized, and your forklift operators become ninjas navigating those lanes. The Win: Unbeatable density for high-volume, uniform SKUs.
- Warehouse Mezzanines Floor (The Vertical Visionary): This is where you literally create new floor space. A Warehouse Mezzanines Floor is a raised platform built within your existing building, effectively adding a second (or even third!) level. You’re building upwards within your vertical cube, unlocking air rights you already pay for. Suddenly, that area above your receiving dock or packing stations becomes prime real estate for offices, light assembly, packing lines, or slower-moving inventory. The Win: Creates entirely new, usable square footage without expanding the building footprint. Ideal for freeing up valuable ground floor space for core operations.
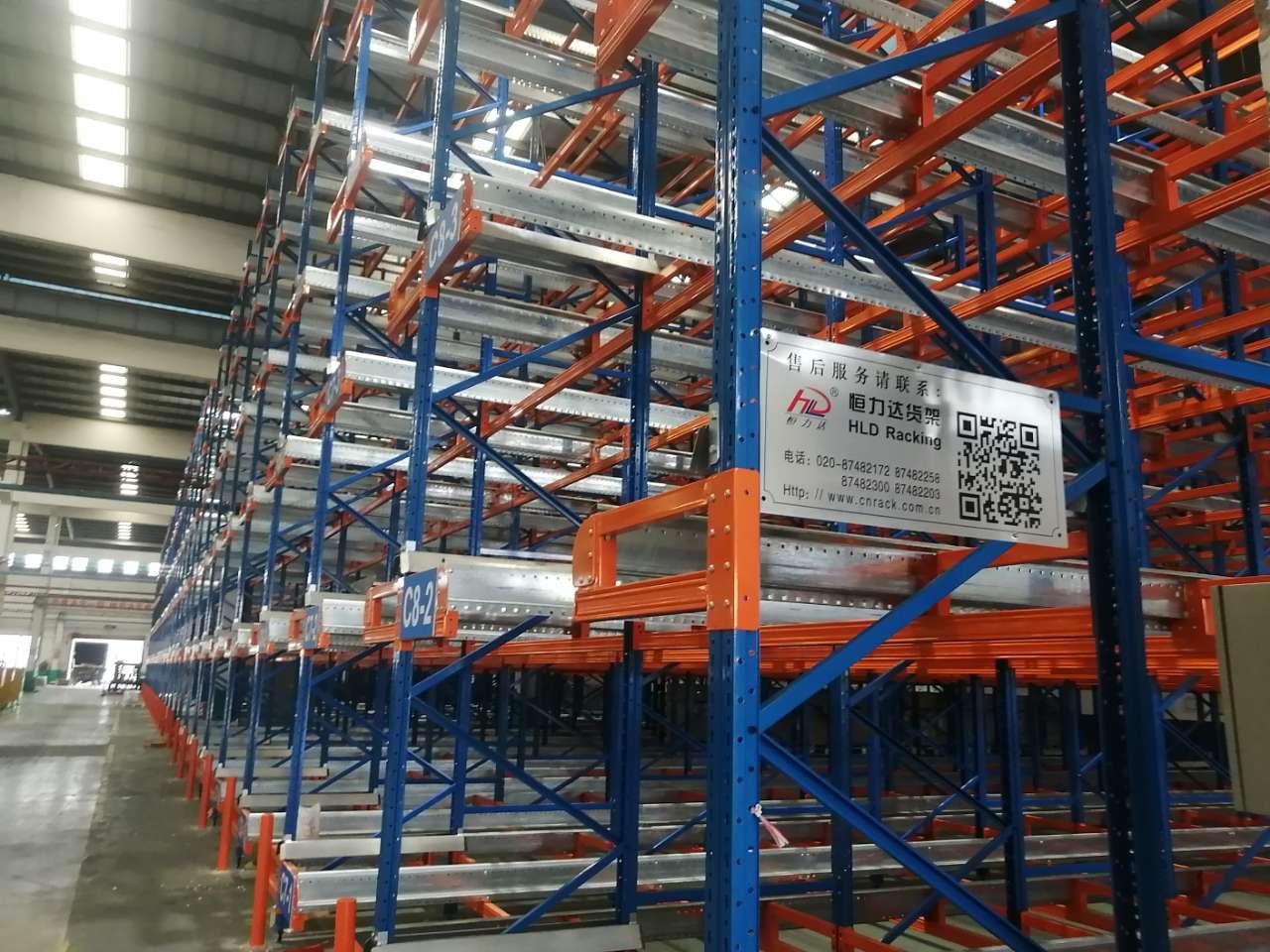
Round 2: The Cost Clash – Upfront Sticker vs. Long-Term Value
- Regular Shelving: Generally, the upfront cost per square foot of storage space is lower for shelving. You buy the racks, install them, and you're good to go (for pallet racking, factor in floor anchors and potential sprinkler mods). It’s a relatively straightforward capital expense. The Catch: You’re only getting storage. If you need space for people or processes, shelving doesn’t magically create that.
- Warehouse Mezzanines Floor: Yeah, the initial investment for a Warehouse Mezzanines Floor is usually higher. You’re essentially building a mini-floor – structural steel, decking, stairs, railings, integrating with fire protection, maybe even lighting and HVAC up there. It’s a more complex project. The Win: BUT, you’re not just paying for storage; you’re paying for usable floor space – the most valuable commodity in any warehouse. This space can house revenue-generating activities (like kitting/packing), essential support functions (offices, break rooms), or consolidate operations, potentially eliminating the need for expensive off-site space. The ROI often comes from operational efficiency gains and avoiding costly expansion/relocation.
Round 3: Flexibility & Function – Static Storage vs. Dynamic Space
- Regular Shelving: Shelving is purpose-built for storage. While you can reconfigure layouts (with some effort), its function is pretty singular: hold stuff. Moving shelving significantly is a major project. It’s static. Great for stable inventory profiles.
- Warehouse Mezzanines Floor: Here’s where Warehouse Mezzanines Floor solutions often shine in versatility. That new platform isn’t just for boxes! It can be:Office Space: Get management off the noisy floor.Light Manufacturing/Assembly: Dedicated space for value-add.Packing & Shipping Stations: Consolidate outbound logistics overhead.Quality Control Labs: Clean, controlled space.Employee Amenities: Break rooms, locker rooms.Slower-Moving Inventory Storage: Free up prime ground-floor real estate for fast movers.The floor space is inherently more flexible. You can partition it, move workstations, and repurpose it much more easily than reconfiguring massive rack structures. Need to change its use in 5 years? Much more feasible.
Round 4: Installation & Disruption – Quick Fix vs. Strategic Build
- Regular Shelving: Installation is usually faster and causes less operational disruption. You can often install sections piecemeal while operations continue nearby. Getting pallet racking up is a well-oiled process.
- Warehouse Mezzanines Floor: Installing a Warehouse Mezzanines Floor is a bigger deal. It requires careful engineering (load capacities, seismic considerations if applicable), significant construction work, coordination with fire safety (sprinklers, fire ratings), and potentially integrating utilities. This means more planning, longer installation time, and likely more disruption to your current operations in the installation zone. You need a clear plan and timeline.
Round 5: The Heavyweight Championship – What Are You Storing?
- Regular Shelving: Shelving, especially structural pallet racking, is designed to handle serious weight – multiple tons per pallet position. If you’re storing dense, heavy pallets (think steel, liquids, machinery), robust shelving/racking is often the only practical solution. Warehouse Mezzanines Floor structures have weight limits per square foot, and extremely heavy loads might make them impractical or prohibitively expensive.
- Warehouse Mezzanines Floor: Warehouse Mezzanines Floor systems are incredibly strong, but they have defined load capacities (e.g., 125 PSF, 250 PSF, even higher for specialized industrial mezzanines). They excel for:Lighter inventory (retail goods, packaged items).People-intensive activities (offices, light assembly).Equipment that doesn't require massive foundations (packing machines, conveyors).Storing bulky but lightweight items.Always, always engineer the mezzanine for your specific planned loads, including dynamic loads (people moving, equipment vibration).
So, When Does a Warehouse Mezzanines Floor Steal the Show?
A Warehouse Mezzanines Floor becomes the clear frontrunner when:
- You're Truly Out of Floor Space: You physically can't expand outwards, and your vertical cube above 12-15 feet is wasted air. Building up internally is your only viable option.
- You Need More Than Just Storage: If you require space for offices, production, packing, or other operational functions within the warehouse envelope, a mezzanine creates the necessary floor area.
- Ground Floor Real Estate is Gold: Freeing up your most accessible, dock-proximate space for high-velocity receiving, shipping, or fast-moving pick faces provides huge efficiency gains. Push slower ops or storage upstairs.
- You Want Long-Term Flexibility: Anticipating future changes in process or space needs? The inherent adaptability of a Warehouse Mezzanines Floor platform is a major advantage.
- Relocating or Expanding is Painful/Expensive: If moving to a bigger building is a nightmare (cost, location, downtime), a mezzanine can be a cost-effective way to stay put and grow.
And When Should You Stick with Good Ol' Shelving?
Shelving remains the undisputed champ when:
- Pure, High-Density Storage is King: Your primary need is storing the maximum number of pallets or bins in the smallest footprint. Mezzanines involve stairs/elevators and access points that reduce pure storage density below.
- Budget is Extremely Tight Upfront: If capital is severely limited and you only need storage now, shelving is usually the cheaper initial solution.
- You Deal with Super-Heavy Loads: Storing massive machinery parts or extremely dense materials? Heavy-duty racking is likely the only safe and economical choice.
- You Need Minimal Disruption Now: Need storage capacity yesterday? Shelving installs faster than a major Warehouse Mezzanines Floor project.
- Your Ceilings Are Low: If your clear height is already maxed out with racking or is very low (e.g., under 16-18 feet), adding a functional mezzanine might be impossible or impractical.
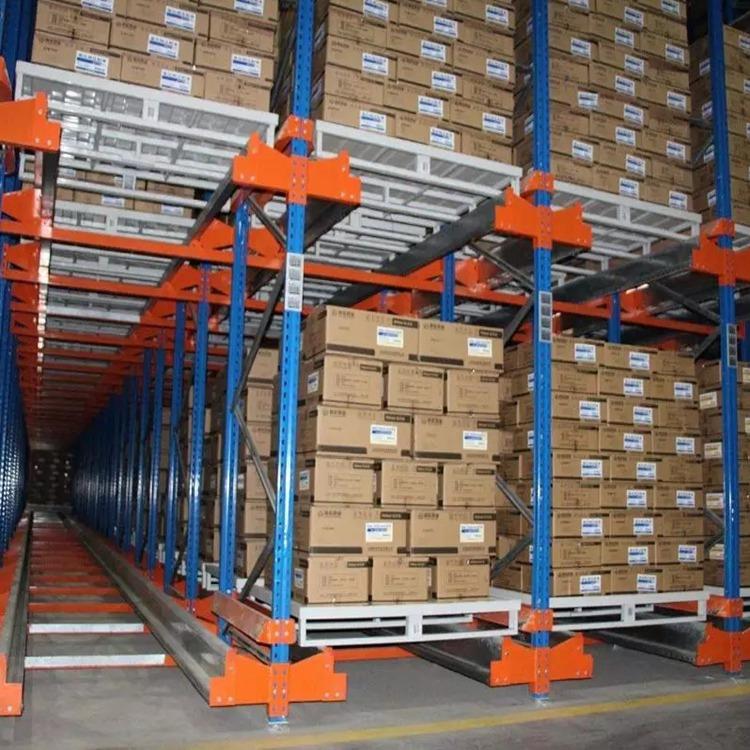
The Smart Play: Why Not Both? (Seriously!)
Here’s the pro tip: It’s rarely an either/or situation. The most optimized warehouses often leverage both strategically:
- Ground Floor: High-bay pallet racking for fast-moving bulk storage, dock doors, receiving/shipping areas, primary pick modules. Maximize density and flow.
- Warehouse Mezzanines Floor Level: Offices overlooking the floor, packing/shipping stations fed by conveyors from below, light assembly/kitting areas, quality control labs, break rooms, or storage for slower-moving SKUs, seasonal items, or packing materials. Use the vertical space created by high shelving for non-storage functions.
Key Considerations Before You Jump (or Build Up)
- Building Structure & Codes: This is NON-NEGOTIABLE. Will your existing floor support the concentrated loads of the mezzanine columns? What are local building codes and fire regulations (egress, sprinklers, fire ratings)? You need a qualified structural engineer and architect familiar with industrial codes. Permitting is essential.
- Load Capacity: Be brutally honest about everything that will go on the mezzanine – people, equipment, inventory, even filing cabinets. Don't forget dynamic loads (forklifts driving near columns?).
- Access: Stairs are mandatory. Elevators or material lifts add cost but are crucial for moving goods efficiently. How will people and product flow?
- Utilities: Need power, lighting, data, compressed air, or HVAC up there? Factor in the cost and complexity of running these.
- Future-Proofing: Design for potential future expansion or reconfiguration. Modular Warehouse Mezzanines Floor systems offer more flexibility than welded ones.
The Bottom Line: It’s About Your Operation’s DNA
There’s no single "better" option between regular shelving and a Warehouse Mezzanines Floor. The winner is determined by your unique operation:
- What you’re storing (weight, type, velocity).
- How you’re using the space (pure storage vs. multi-function).
- Where your bottlenecks are (floor space vs. vertical space).
- What your budget allows (upfront vs. long-term ROI).
- What your building can physically handle.
Regular shelving is your reliable workhorse for high-density, heavy-duty storage. A Warehouse Mezzanines Floor is your strategic space-creator, unlocking unrealized potential within your four walls for people, processes, and lighter storage.
The smartest warehouse managers don't just choose one; they analyze their needs down to the square foot and strategically deploy both solutions to build the most efficient, cost-effective, and adaptable operation possible.