Let's face it, warehouse and industrial space is expensive. Really expensive. And as your business grows, that square footage seems to shrink faster than your coffee break. When expanding outwards isn't an option (or is just plain budget-breaking), smart operators look upwards. Enter the Heavy Duty Mezzanine. This isn't your flimsy storage loft; we're talking serious structural steel platforms built to handle pallets, machinery, production lines, and serious foot traffic. But like any major warehouse investment, it's not a one-size-fits-all slam dunk. Let's break down the real-world pros and cons to see if a Heavy Duty Mezzanine is your space-saving superhero or a potential headache.
The Shiny Upside: Why Heavy Duty Mezzanines Are Tempting
- Unlock Massive Vertical Real Estate (The Big Kahuna Pro): This is the #1 reason folks go down this path. You're literally creating new, usable floor space out of thin air – space you're already paying rent or mortgage on. Instead of leasing a bigger building (with all the moving costs, higher rent, and potential location compromises), you maximize what you have. A well-designed Heavy Duty Mezzanine can often double your effective floor area. That's game-changing for storage, production, offices, or packing stations.
- Serious Cost Savings (Long-Term Wallet Relief): While the upfront cost isn't trivial (we'll get to that), it's almost always significantly cheaper per square foot than acquiring, building out, or moving to a new facility. You avoid skyrocketing lease rates in new locations, massive moving disruptions, and the hidden costs of setting up a whole new operation. The ROI on a Heavy Duty Mezzanine often makes CFOs smile.
- Operational Efficiency on Steroids: Imagine moving slow-moving inventory or bulky raw materials up and off your prime ground-floor space. Suddenly, your main floor is freed up for faster-moving goods, value-added services, or smoother workflow. You can design workflows vertically – raw materials staged above feeding a production line below, or packing/shipping on the mezzanine directly over receiving docks. A Heavy Duty Mezzanine lets you optimize your layout logically.
- Scalability & Flexibility (Future-Proofing): Need more space in 18 months? A quality Heavy Duty Mezzanine system is often designed to be reconfigured, expanded, or even relocated (though moving them is a project!). You can add sections, change decking, or modify access points much more easily than renovating a building or moving. This modularity is a huge asset for growing or changing businesses.
- Preserves Precious Floor Space: By moving storage, support functions, or even offices upstairs, you keep your main operational floor clear for core activities like manufacturing, assembly, order picking, or loading docks. No more tripping over stored pallets or squeezing around office walls.
- Improved Organization & Inventory Control: Dedicated mezzanine levels allow for better segregation of inventory types, stages of production, or different product lines. This can lead to easier cycle counting, better FIFO (First-In, First-Out) management, and overall cleaner, more organized operations.
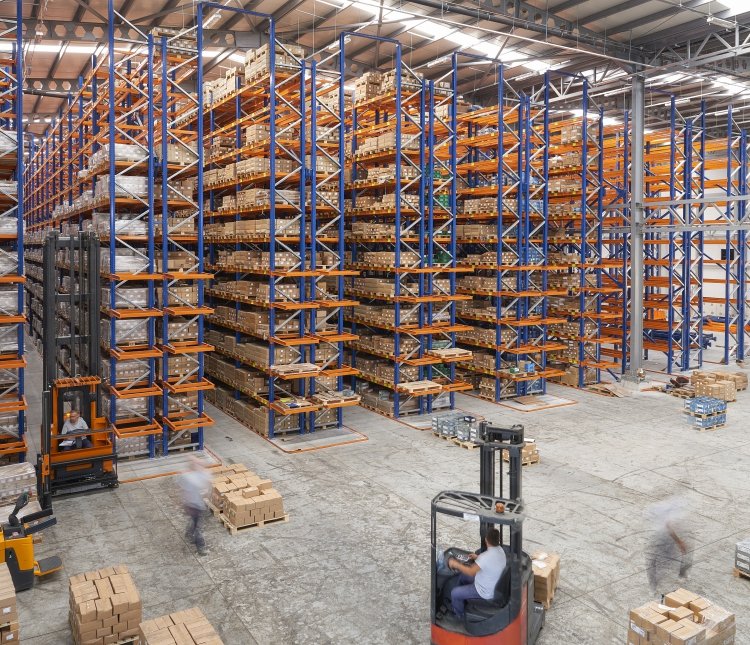
The Gritty Downside: Challenges & Considerations of Heavy Duty Mezzanines
- Significant Upfront Investment (The Sticker Shock): Let's be real: a true Heavy Duty Mezzanine built to industrial standards with proper safety features (guardrails, stairs, fire protection), capable of holding thousands of pounds per square foot, is a major capital expense. The cost involves engineering, materials (heavy steel), fabrication, installation, decking, stairs/ladders, safety systems, and potentially lighting/utilities. It's cheaper than moving, but it ain't pocket change.
- Complex Engineering & Permitting Headaches: This isn't DIY territory. A Heavy Duty Mezzanine requires meticulous structural engineering to ensure it can handle the intended loads and that your existing building floor can support the concentrated point loads of the mezzanine's columns. You'll also be diving deep into building codes (IBC – International Building Code), fire codes (sprinkler requirements underneath and potentially on the deck itself), and OSHA regulations. Permitting can be time-consuming and complex. Don't underestimate this phase!
- Disruption During Installation: Building a Heavy Duty Mezzanine inside an active warehouse or factory is disruptive. Expect noise, dust, equipment moving around, and potentially areas being cordoned off for safety. Careful planning and phasing are crucial to minimize downtime, but some interruption is inevitable. Installation can take weeks or even months for very large systems.
- Impact on Building Systems: That awesome new space overhead? It affects what's below and around it. Key considerations include:Sprinkler Systems: Fire codes almost always require sprinklers under the mezzanine deck and often on the deck itself if occupied or storing combustibles. This can mean significant modifications to your existing sprinkler system.Lighting: The mezzanine itself will need lighting, and it will cast shadows below. You'll likely need to redesign or augment your main floor lighting.HVAC/Ventilation: If occupied, the mezzanine level may need heating, cooling, or ventilation, requiring ductwork runs.Clearance: Ensure enough headroom below the mezzanine for operations (forklifts, personnel) and on the mezzanine for its intended use. Don't forget about existing lights, ductwork, or trusses!
- Material Handling Challenges (The Vertical Tax): Getting stuff up and down is the operational cost of vertical space. You'll need efficient solutions:Stairs: Essential for personnel, but slow for moving goods.Industrial Ladders: For occasional access, but not for heavy items.Conveyors: Great for consistent flow of specific items, but expensive to install.Lifts (Material or Personnel): Versatile but require space and maintenance.Integrating Forklifts: Some heavy duty designs allow for dedicated forklift ramps or even integrate with building docks on multiple levels (more complex and expensive). Every trip up or down takes time and resources.
- Potential for "Cave Effect" Below: While freeing up floor space, a large mezzanine can make the area underneath feel darker, more enclosed, and potentially less pleasant for workers or operations that remain there. Careful lighting design is critical.
- Structural Load on Existing Floor: This is paramount. Your existing concrete slab must be thick enough, strong enough, and in good condition to support the immense point loads transferred by the mezzanine columns. Core drilling and structural analysis are non-negotiable steps before design even begins. A slab that seems fine for forklifts might crumble under concentrated mezzanine loads. Retrofitting the slab is possible but adds major cost and complexity.
- Thermal Bridging (Potential Comfort Issue): In heated/cooled spaces, large steel structures like a Heavy Duty Mezzanine can act as "thermal bridges," potentially causing localized cold spots (in winter) or heat gain (in summer) where the steel connects to the exterior walls or roof. Insulation strategies might be needed.
Making the Smart Choice: It's All About Context
So, is a Heavy Duty Mezzanine the right move? The answer, frustratingly, is "it depends."
- GO for it if: Your current building footprint is constrained, leasing/buying more space is prohibitively expensive, your floor slab is proven strong enough, you have sufficient ceiling height (typically at least 16-18 feet clear to the bottom of roof trusses/obstructions for a usable mezzanine), your operations can handle vertical material movement, and you have the capital budget and tolerance for the project timeline/disruption. The long-term space and cost benefits can be phenomenal.
- Think VERY carefully or explore alternatives if: Your ceiling height is low, your existing floor slab is weak or unknown, your budget is razor-thin, you absolutely cannot tolerate operational disruption, your material flow is extremely horizontal and high-speed, or permitting/fire code hurdles look insurmountably complex. Alternatives might include ultra-dense shelving systems (like mobile aisles), off-site storage (though this adds transport costs/time), or a more painful but potentially simpler relocation.
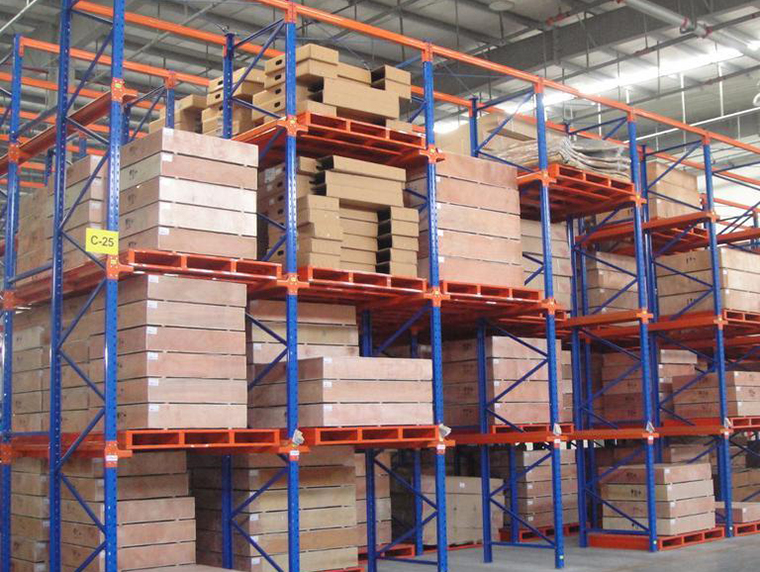
Partner Smart: Your Heavy Duty Mezzanine Success Formula
- Hire Experts: Don't cheap out. Work with reputable Heavy Duty Mezzanine manufacturers and installers who have deep experience with engineering, local codes, and industrial applications. They should conduct a thorough site survey and structural analysis first.
- Engineer First, Dream Second: Let the structural realities and code requirements dictate the feasible design, not the other way around. Your vision needs to fit the physics and the law.
- Plan for EVERYTHING: Budget meticulously, including engineering, permitting, all materials, installation, utility modifications (sprinklers, lights, HVAC), safety features, and contingency (at least 10-15%). Map out the installation phasing and disruption mitigation strategies with your team and the vendor.
- Prioritize Safety & Compliance: This is non-negotiable. Guardrails, toe kicks, stair specifications, load signage, fire protection – do it all, do it right, from day one. OSHA and your local fire marshal will notice.
- Optimize Material Flow: Design the mezzanine layout and the vertical access points (stairs, lifts, conveyors) together with your operational workflow in mind. How will stuff actually get up and down efficiently every day?
The Bottom Line
A Heavy Duty Mezzanine is a powerful tool for unlocking serious vertical potential within your existing four walls. The benefits – massive space creation, long-term cost savings, and operational optimization – are incredibly compelling for the right situation. However, the path is paved with significant upfront costs, complex engineering and permitting, potential disruption, and critical considerations around building systems and material handling. It’s not a casual purchase; it’s a major industrial project.
Carefully weigh the pros and cons against your specific facility, budget, operations, and growth plans. Do your due diligence on your building's structural capacity and the local regulatory landscape. If the stars align, a Heavy Duty Mezzanine can be the strategic investment that fuels your growth for years to come, turning your cramped warehouse into a model of vertical efficiency. Just go in with your eyes wide open and the right experts by your side. Ready to explore your vertical potential? Get those ceiling heights measured and start talking to qualified Heavy Duty Mezzanine specialists!